Sandvik Coromant’s “digital thread” which spans throughout its factory in Gimo, Sweden, has seen it win international recognition from the World Economic Forum (WEF).
Part of Swedish global industrial engineering group Sandvik, Sandvik Coromant is at the forefront of manufacturing tools and machining solutions that drive industry standards and innovations in the metalworking industry.
The raised labour productivity in the company’s Gimo plant as a result of extensive automation saw the WEF name it a ‘Lighthouse of the Fourth Industrial Revolution’ for factories which have successfully implemented Fourth Industrial Revolution technologies. Joining WEF’s ‘Factories of the Future’ network, the Gimo plant was one of the 1,000 factories on the shortlist drawn up by WEF – which eventually selected 16 factories.
With its machines and robots programmed with a high level of autonomy, Sandvik Coromant is even able to run its Gimo factory unmanned for a significant amount of time. WEF found that over 70 percent of businesses investing in technologies such as big data analytics, artificial intelligence (AI) or 3D printing are not able to take the projects beyond pilot phase – making Sandvik Coromant’s achievement, and that of the other 15 ‘Factories of the Future’, all the more impressive.
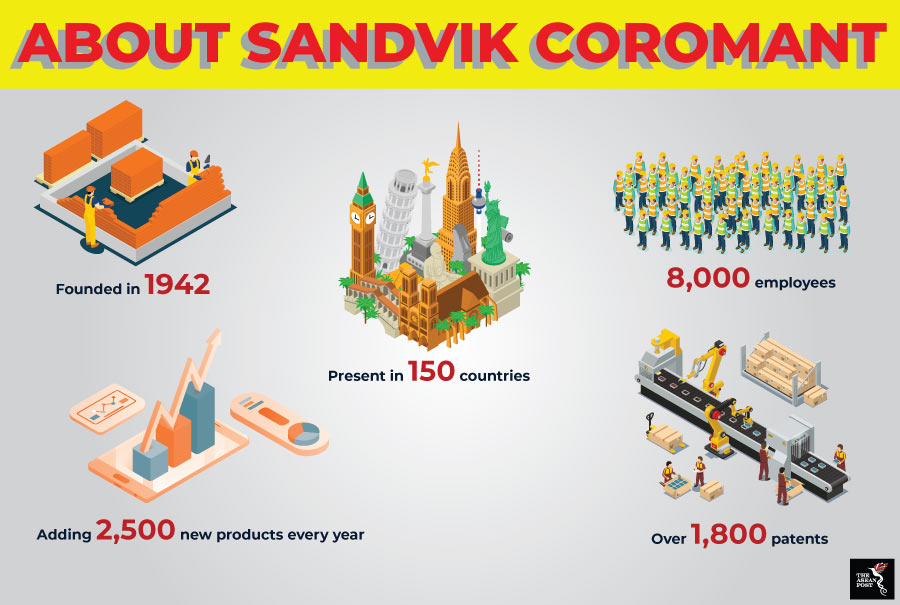
‘It starts with design’
In an exclusive interview with The ASEAN Post, Sandvik Coromant’s Manager of Computer Aided Process Planning (CAPP) and Computer Aided Manufacturing (CAM) Automation, Simon Smedberg, explained that their “digital thread” starts long before actual production.
“It starts with design, and we do not use any static drawings or 3D models to feed our production. Instead, we have a design program that creates a computer-aided design (CAD) model for each specific order, and this process is fully autonomous,” he said.
“In similar fashion, process planning, machine programs, production parameters, drawings, etc. are created autonomously for each order. All of this happens within a few minutes of an order being created and allows for customised products to be ordered and handled the same way we would any standard order,” he added.
This has an enormous impact on Sandvik Coromant’s engineering, allowing it to introduce new products at a rate that would not be possible with traditional methods as they do not need to manually create and maintain product and production data for the 15,000 different standard articles they produce.
On the shop floor, this means that the machine program can be automatically transferred to the correct machine together with a set of parameters for the robot that serves it. The combination of one or more machines and robots is called a cell, and cells have a high level of autonomy – which means, for example, tool changes can happen autonomously. This allows for a larger number of machines per operator and unmanned factory operations.
Automation in ASEAN
Many ASEAN countries already have Industry 4.0 blueprints to help ease their digital transition and spur growth. However, if not managed properly, these disruptive technologies could lead to unemployment. The Thailand Development Research Institute (TDRI), for example, last year stated that the country is on track to lose as many as three million jobs over the next 20 years if it fails to adapt to changes such as robotics and AI.
Textiles, apparel, and footwear manufacturing are key segments within ASEAN, accounting for more than nine million jobs, or three out of 10 wage employees. A report titled ‘The future of ASEAN – Time to act,’ published in May 2018 by audit firm PricewaterhouseCoopers stated that the above industries – where labour-intensive production lines make for low productivity – have placed employees at high risk of displacement with the uptake of automation, especially over the next decade.
In the factories of the future, those who are able to adapt working alongside machines will find renewed opportunities – while those without digital skills and those who perform repetitive tasks could find themselves at risk of unemployment or falling wages.
As automation becomes more attractive due to increases in productivity and lower operational costs, more of ASEAN’s advanced economies will start introducing it according to consultants McKinsey & Company as reported in Singaporean media last September. But even with automation, the demand for work and workers could increase as economies grow, partly fuelled by productivity growth enabled by technological progress.
Related articles:
Can Industry 4.0 revolutionise manufacturing?